We Got Your Back-up, with Uninterruptible Service.
Our national infrastructure allows us to serve you 24 hours a day, 7 days a week, 365 days a year. Ready for any emergency scenario or catastrophic event we can deploy skilled engineers to provide immediate repairs or installations of critical equipment to restore power.
Our on-call team provides quality work at every level of service. We are available for consultations for projects including facility design and equipment replacement.
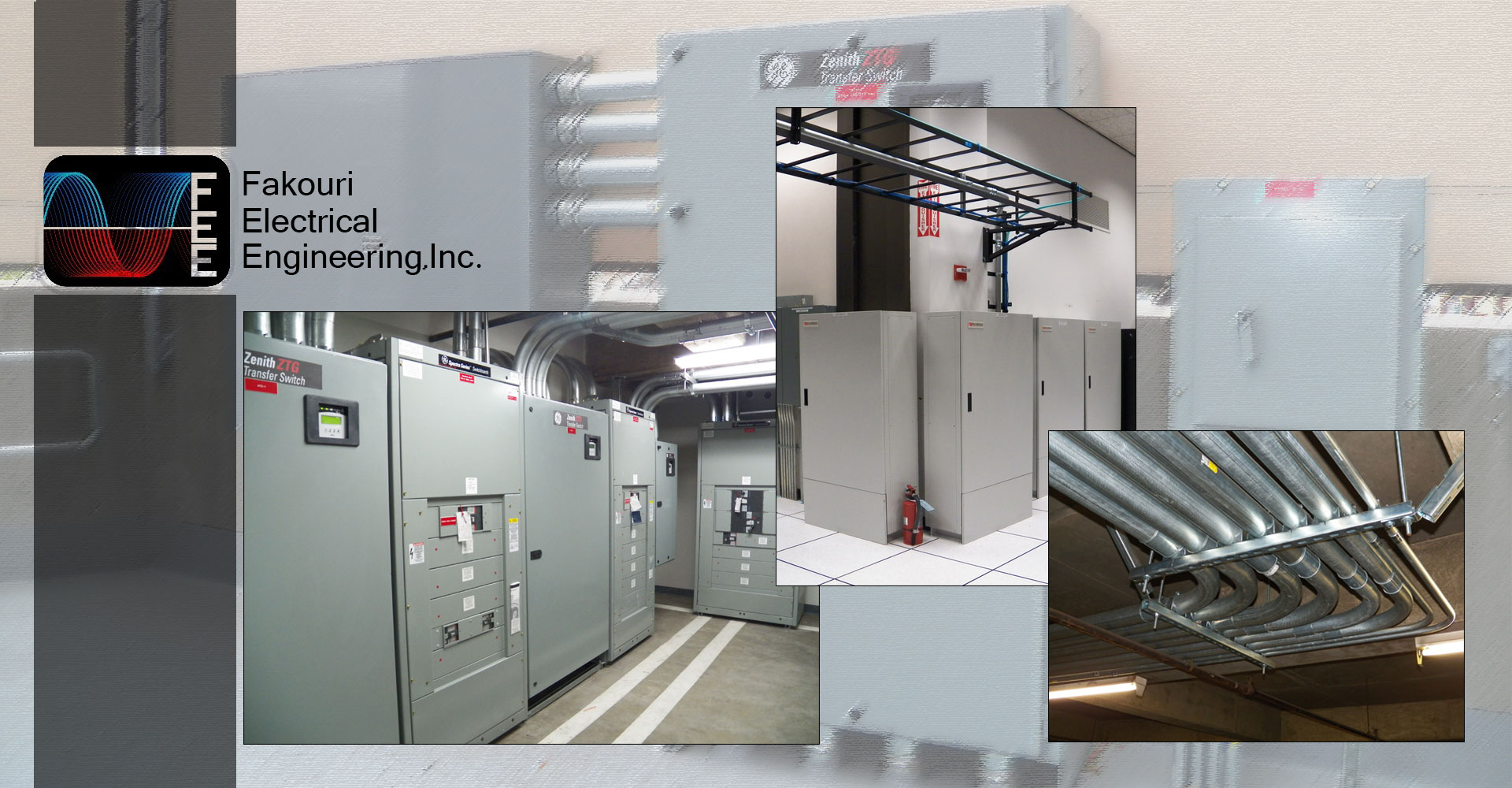
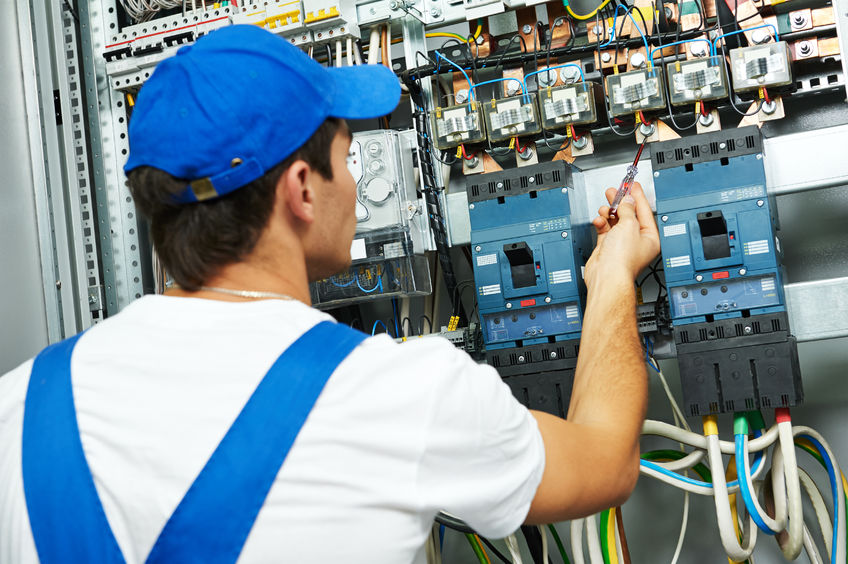
Emergency Coverage. All Day, Every Day.
In addition to our comprehensive proactive maintenance program, we provide emergency critical power services to data centers and facilities. Our 24/7 response team provides immediate resolutions to emergencies and catastrophic events, restoring peace of mind when you need it most. Our experience in data center and facility critical environments guarantees your satisfaction.
As with many emergencies, parts for equipment is essential for prompt repair and resolution. With our in-house inventory of Uninterruptible Power Supplies and critical equipment, we can provide parts immediately any time, any day. In many facilities, FEE provides spare parts on-site for legacy equipment and parts for equipment with long lead times.
Our headquarters and facilities located throughout the U.S. are stocked with parts and components for most UPS systems, and UPS related equipment. We also stock refurbished total Uninterruptible Power Supply systems, PDU’s, circuit breakers, cables, batteries, and key components of equipment and legacy units, for immediate deployment to catastrophic events.
Account Management in a Holistic Service Facility
Our in-house team ensures a dedicated, single point of contact with experienced technical personnel for multiple equipment types. We provide service to various manufacturers and vintage Uninterruptible Power Supply systems which may no longer be supported by the manufacturer.
Method of Procedures (MOP) & Singles Line Diagrams
As part of our safety and service protocols, prior to a scheduled service we will produce a detailed MOP outlining:
- Equipment
- Maintenance Procedures
- Materials
- Safety Procedures
- Scope Of Work
Upon completion, our single line diagram and verification of operational procedures are provided.
Root Cause Analysis (RCA)
Root Cause Analysis of component failures are submitted within 3-5 days to identify trend analysis of failed components.
Asset Management
Our web portal allows you to review field service reports, MOP’s, and equipment status.
Critical Action Notices (CAN)
Immediate Critical Action Notices report both verbal and written should any condition jeopardize operations.
Training
Integration within the data center, provided for your convenience.